Rare people have not heard about the negative impact of waste oil reclamation on the environment. But the lack of legal acts, points of collection/processing, as well as inadequate use of oil recycling and oil reclamation tion methods often lead towaste oil reclamation being simply drained. What follows it – is air and water pollution and soil degradation.
What is “waste oil”? It is a mineral or synthetic oil, polluted with physical and (or) chemical impurities incompatible with further use. To fully understand the extent of environmental disaster (and it is thousands of tons of wastes produced by mankind in a year), it is enough to recall the sources of waste oil reclamation – they are ordinary consumers, various production, service stations, transformer stations, etc.
Each country has its own regulatory document, with a list of substances for further processing. There cannot be a universal list, but oils and coolants (GM), most commonly appearing in this documentation are:
- used engine oils and coolants (transmission, engine and hydraulic oils, brake fluid);
- waste industrial oils (compressor, bearing, turbine, cable, hydraulic and electrical insulating oils, lubricants, coolants, etc.).
If you look at the problem globally: in 2010 the world consumed around 42 million tons of petroleum oil. The forecast for 2016 is 45 million altogether. Not more than 50% of waste oils are collected for recycling or recovery. It is clear that in order to avoid global ecological catastrophe all the countries should try to keep this rate at maximum.
Only competent collecting and recycling of waste materials will preserve Mother Nature, and save financial resources. Especially the regeneration is relevant for the countries that are importing petroleum products. The figures show that: production of 1 gallon of fresh oil requires 67 gallons of crude oil or 1.6 gallons of recycled oil. The economic benefits are obvious.
Very often, the terms “regeneration”, “recovery” and “cleaning” are also used together with “clarification of waste oil.” In fact, they are similar processes, achieved using the same operations, but with a completely different purpose. If oil recondition is carried out to obtain a product with properties similar to the original, bleaching gives oil a better presentation. In fact, the clarification – it is not only a change in the color of oil, but also it is a cleaning process, because to get the desired color, the resin and various petrol impurities should be removed. Also at clarification waste oil reclamation is cleaned from water and solids.
Naturally, clarified oil is valued much higher than not clarified. This is due to much greater scope of its application. For example, such oil may be used for impregnating wooden windows. Dark oil in this case is not suitable, since it would take longer to soak in, giving the window odor and coloring it in black.
Let’s consider the most often used technologies of clarification of waste oil.
Settling – is the simplest method with natural precipitation of harmful impurities under the influence of gravitational forces. The length of the process depends on the degree of contaminations in oil.
If after settling a desired color is not achieved, it is recommended to use a centrifugal filtration and purification.
Filtration removes mechanical impurities and resinous compounds by passing waste oil through special filters. In order to improve the quality of cleaning – a multi-stage filtration (coarse and fine) can be used.
Centrifuges are used to carry out centrifugal purification. This approach is based on heterogeneity of mixture. It separates different fractions of oil. Centrifugal cleaning is considered to be one of the most effective methods for removing water and mechanical impurities.
If, after filtration and centrifugation the desired color of oil was not achieved, the physico-chemical methods are used: coagulation, adsorption, ion exchange or selective cleaning.
Coagulation – is, in fact, an artificial enlargement of particles, which is achieved by introducing special substances into oil – coagulants. The entire process lasts 20-30 minutes, after which the large impurities are removed from oil by settling, filtration or centrifugation.
Adsorption treatment is carried out using the properties of certain substances of natural (clays) and artificial (silica gel) origin. They trap dirt on the outer surface of their pellets and the inner surface of capillaries that are penetrating granules.
Ion exchange purification – a replacement of contaminants with ions (ion-exchange resins). Ion exchangers are mixed in oil where mobile ions are replaced with ion exchangers. Ion exchange purification removes acidic substances, but does not affect the resins.
Selective treatment – has a selective effect on the unwanted components of oil. Phenol or furfural may be used as a solvent.
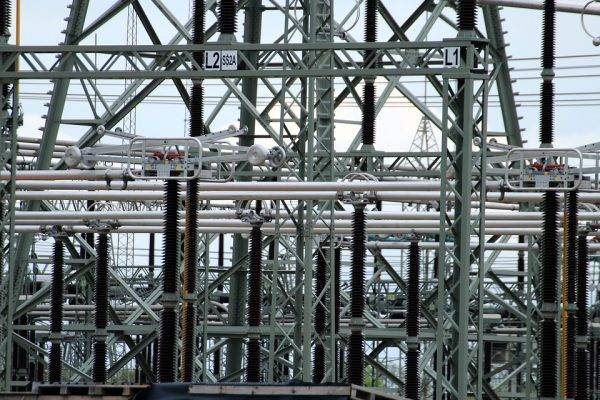
waste oil reclamation
There are also chemical methods of clarification of waste oil. They provide deep cleaning, but are technically complex to implement and quite expensive.