Cmm-4/7 Mobile Oil Plant
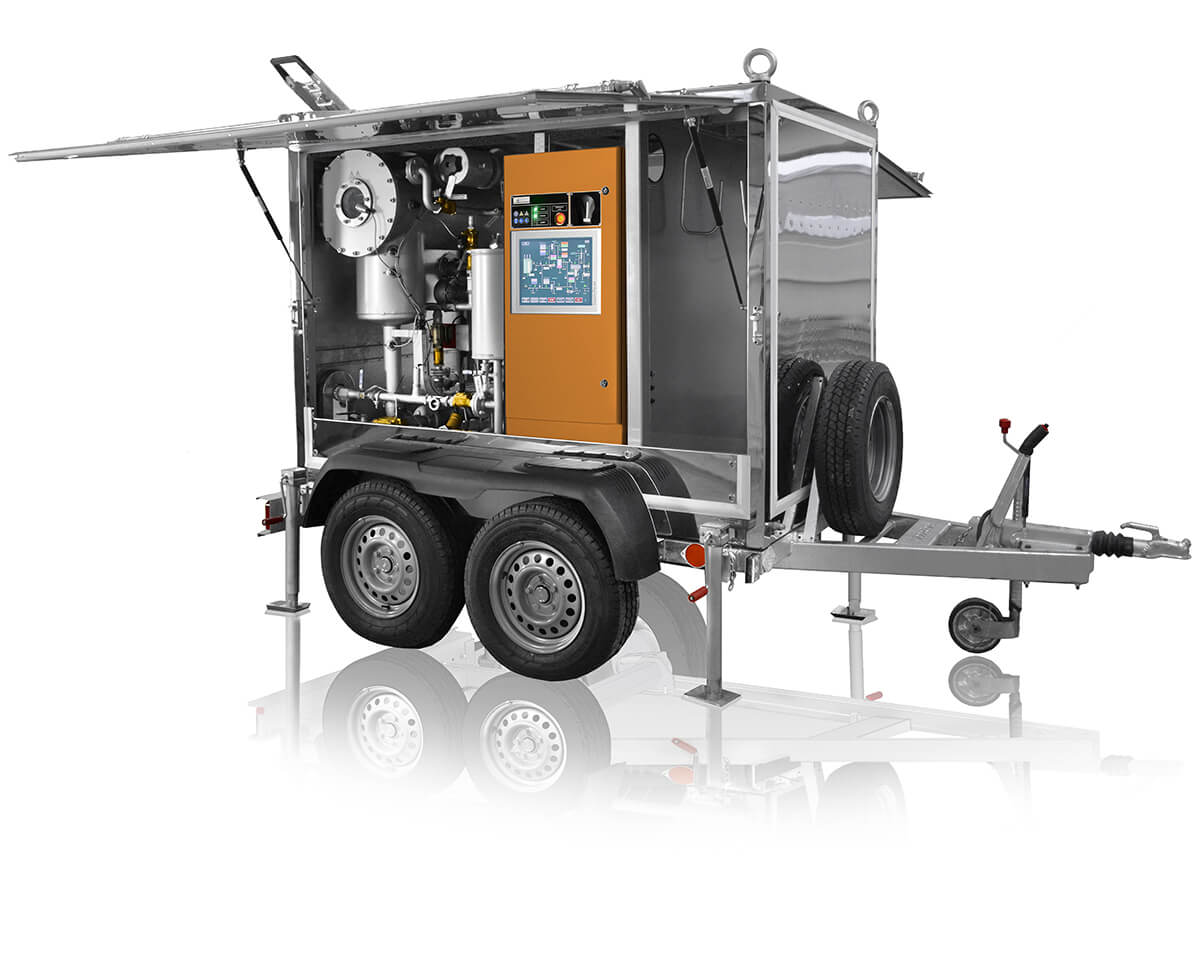
- Removes Water from 100 ppm down to 10 ppm and from 50 ppm to 5 ppm in a single pass (ASTM method D-1533)
- Reduces Gas content from fully saturated with air (10 to 12% by volume) to less than 0.1% (ASTM D-2945)
- Removes Particulate Matter to 5 microns as standard or down to 0.3 micron (optional)
- Improves dielectric strength up to 75 kV
№ |
Specifications |
Value |
1 |
Production capacity, m3/h: | |
– thermo-vacuum mode | 4 | |
– heating and filtration mode | 6 | |
2 |
Treated oil parameters: | |
– gas content, %, maximum | 0.1 | |
– water content, ppm, maximum | 5.0 | |
– purity class (ISO 4406), minimum | 9 (-/15/12) | |
3 |
Nominal filtration rate, mkm | 0.3… 5 |
4 |
Outlet oil temperature, °С | 60 |
5 |
Oil Pressure on outlet, Mpa, minimum | 0.15 |
6 |
Heater power consumption,kW, maximum | 50 |
7 |
Total Power Consumption, kW | 60 |
8 |
Vacuum level in degassing mode, Pa, minimum | 267 |
9 |
Electrical outlet parameters 50/60 Hz, V | 380/220 |
11 |
Dimensions, mm, maximum length/width/height, mm | 1625/1225/1686 |
11 |
Weight, kg, maximum | 900 |
The GlobeCore CMM 4 m3/h – is a High Vacuum De-gasser designed for the removal of solid particles, free and dissolved water, and gases from transformer oil, lubricating oil, turbine oil, and compressor oil.
The GlobeCore CMM 4 m3/h unit is able to process oil on a “tank to tank” basis or directly on energized or de-energized transformers. Trolley or roadworthy trailer mounted, semi-automated, fully automated (PLC controlled) and explosion proof versions of this unit are available. Optional equipment includes moisture probes, flow meter with a totalizer and 0.3 micron fine oil filter.
GLOBECORE OIL PURIFICATION PLANT COMPONENT DESCRIPTION
Vacuum Chamber
Indetification Key: 1– column;2– oil inlet; 3– vacuum pump connection; 4– oil outlet; 5– drainage; 6- coalescers; 7– sight glass; 8– lighting.
Vacuum Chamber Vessels and all internal parts are made of carbon steel and feature Coalescers, Sight Glass, Oil Level Controller, Foam Sensor and Vacuum Gauge. The Vacuum Chamber’s rigid design makes it suitable for stationary or mobile operation. Industrial quality flexible connections are provided to both the outlet and inlet pumps to minimize any possible negative effects of vibration during plant operation and transportation.
Coalescers – built-in coalescers are provided for the maximum exposure of oil to the effects of vacuum. Due to reduced the pressure, dissolved water and gases are vaporized through the secondary chamber and filtered into atmosphere.
Secondary Chamber (Oil Trap) – serves as safety feature to ensure that no oil is pulled into the vacuum pump.
Vacuum Gauge – is provided to monitor Vacuum level in the Vacuum Chamber.
Oil Level Controller – consists of three capacitive probes provided to maintain the required level of oil in the Vacuum Chamber.
Foam Sensor – Rarely, but under certain conditions oil foaming may develop. When the Optical Sensor, installed in the Vacuum Chamber, detects a high level of foam, it will actuate a Solenoid Operated Valve to reduce vacuum and foam level.
Vacuum ports – vacuum connections are provided to pull vacuum on the transformer
Vacuum System
Rotary Vane Positive Displacement Pump
Pumping Speed 100 m3/h
Ultimate pressure 0.5 mbar
Vacuum Booster
Pumping Speed 270 m3/h
Ultimate Pressure 0.01 mbar
Oil Heater
50 kW Oil Heater has a two stage heating facility with 25 kW of power each. Low watt density heating elements (1.2 W/cm2) are used to prevent heat degradation of the oil. The heater is controlled by an electronic temperature controller.
Inlet and Outlet Oil Pumps
“Calpeda Brand” Centrifugal pumps with power consumption of 4 kW and capacity of 12m3/h are utilized to draw oil in and out of the vacuum system. All electric motors are protected by overload detection devices.
Filters
A Mesh Strainer is provided to remove large particles that could cause damage to the Inlet Pump. A Coarse Filter for particles larger than 5 microns is installed at the entry port to the Vacuum Chamber. Oil then receives its final treatment by passing through the Fine Filter designed to remove 99.9% of particles larger than 2 microns or with an optional 1 micron capability.
Instrumentation and Controls
Manometers – are installed to monitor the state of Coarse and Fine Filters.
Temperature controller – receives input data from a temperature sensor and is connected to a control element of the heater.
Measuring and control parameters are pre-set by the manufacturer.
Power and Heating Indicators and Switches, Inlet and Outlet Oil Pumps Switches– are located on the control panel.
Emergency Stop Button – is provided for safe shut down of the plant in case of emergency.
Alarms and Interlocks
GlobeCore CMM oil purification plants feature the following safety devises that ensure simple and reliable operation and will safely shut down the system in case of any alarm situation:
High Level Alarm – will alert plant’s operator by activating sound and light alarms and will shut down the system safely should high level of oil persist.
Low Level Alarm – interlocked with the inlet pump, the low level alarm will safely shut down the plant in case of insufficient oil level.
Flow Sensor – only activates the Heater when oil flow is detected.
Foam Sensor – prevents excessive foaming
Overloads – all motors are protected by overloads detection devices
Alarms – a sound and light alarm with a silence button will alert the plant’s operator of any emergency situations.
OPTIONAL EQUIPMENT
GlobeCore Fuller’s Earth Сartridges (ZP-260)
GlobeCore’s Fuller’s Earth systems are specially engineered to remove soluble contaminants such as acids, waxes, gums, resins, carbon residues and colloidal particles from transformer oil. They are designed for oil polishing after purification. For large quantities of oil, GlobeCore’s regeneration system is recommended.
GlobeCore CMM 4.0 A Flow Diagram
VC– vacuum column; H – oil heater; CP1 – CP2 – oil pumps; MV1– MV17 –manual ball valve; BV1 – BV7 – reverse valve; F1,F2 – cartridge filter; М1 – М4 – manometers; EV1– EV6 – electric valve ; LS1 – LS5 – level sensors; VP1 – vacuum booster; VP2 – vacuum pump; EVM – digital vacuum meter; R – receiver; PF – mesh filter; FS – flow relay; t1–t3 – temperature sensor; CL1 – oil inlet; CL2 – oil outlet; CL3 – oil supply to oil regeneration equipment; CL4 – regenerated oil inlet; AV1 – AV2 – air release valve; LP – leaks collector; AF – air release valve; LC – liquid meter.
Moisture Probe
The transmitter provides on-line transformer oil measurement of both the moisture content and the temperature. The unit comes complete with a display showing the level of moisture in a “ppm” readout
Flowmeter
Influx Florack flowmeter gives a reading in m3/h and totaliser shows the total flow passed in a time through the meter.
Typical Oil Parameters after Tretment with Fuller’s Earth
Parameter | Test Method | Before Reclamation | After Reclamation |
Appearance | Visual | Cloudy Brown | Clear and transparent |
Acid Number, mg KOH/g | IEC 296; ASTM D-664 | 0.63 | 0.01 |
Corrosive Sulphur | ISO 5662;ASTM D-1275 | Present | Absent |
Tangent delta at 90°C | IEC 247; ASTM D-924 | 4.0 | 0.001 |
Oxidation Stability, mg KOH/g | IEC 1125А;IEC 1125B; IP-307 | – | 0.2 |
Surface Tension at 25°C, mN/m | ISO 6295;ASTM D-2285 | 22 | 45 |
PORTABILITY OPTIONS
The GlobeCore CMM Units are mounted on a tandem axle trailer covered with a canvas canopy or enclosed by optional steel sidewalls with lift up doors
GlobeCore also offers a Triple axle semitrailer comprised of a CMM oil purification plant, an on-board generator with fuel tank, and an air conditioned and heated operator’s room.
GlobeCore Worldwide Sales