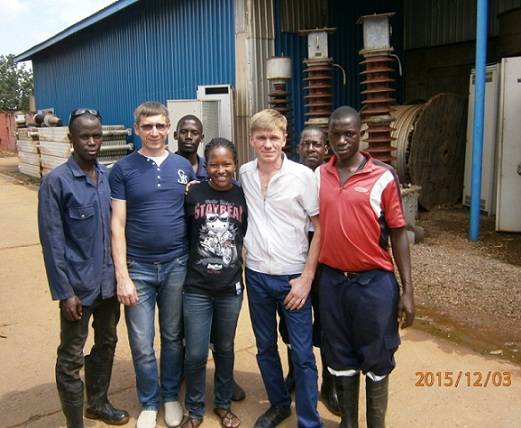
On December 3, 2015 GlobeCore employees successfully completed the commissioning of a new GlobeCore CMM-4D oil degassing unit in Uganda.
The main advantage of the CMM-4D is its versatility. With the CMM-4D unit you can perform the following operations:
- purification of insulating oil by removing mechanical impurities (filtration fineness is 5 microns), water and gases;
- heating of electrical apparatuses with transformer oil;
- vacuum drying of transformers; and
- vacuumizing of equipment.
The principle of operation of the GlobeCore CMM-4D unit is based on the thermal vacuum purification of transformer oil in electric substation. In the vacuum column, the oil is finely atomized. Special filter-activators provide for a larger area of its processing.
The unit can operate in the following modes:
- oil transfer;
- warm-up of transformer at electric substation;
- heated filtration and thermal vacuum purification of the oil; and
- vacuumizing of equipment.
GlobeCore’s CMM-4D unit is easy to operate and maintain and it provides stable processing parameters of transformer oil. With the installed sensors and automation system, you are able to control the oil heating temperature, monitor the presence of oil flow through the heater, protect the heater from overheating, and adjust the heating temperature in accordance with the set mode.
You can order the multifunctional CMM-4D unit for purification and degassing of transformer oil right now by contacting one of the persons on the contact list. Remember that we are always ready to answer your questions.